In today’s competitive manufacturing environment, the ability to rapidly develop and refine prototypes is crucial to delivering high-quality products efficiently. For companies like Wiesel, which specializes in industrial prototyping and large-scale manufacturing, the intersection of these two processes is key to driving innovation, reducing costs, and ensuring robust production pipelines. This article explores the role of industrial prototyping in large-scale manufacturing and how Wiesel’s expertise benefits various industries by streamlining product development and enhancing manufacturing efficiency.
The Role of Industrial Prototyping in Manufacturing
Industrial prototyping is the bridge between design and manufacturing. It enables companies to create tangible models of products or components before committing to full-scale production. This stage is critical as it allows engineers and designers to test and refine the functionality, durability, and manufacturability of products in a real-world context. At Wiesel, the prototyping process is optimized with advanced materials and cutting-edge technologies, ensuring that prototypes are as close to the final production model as possible.
For industries like automotive, aerospace, consumer electronics, and medical devices, the reliability of each part is crucial. A well-executed prototyping phase can highlight potential issues, allowing engineers to address these concerns before mass production begins. Wiesel’s prototyping solutions help companies minimize waste, reduce costly redesigns, and shorten time-to-market, ensuring that only the best possible versions of products make it to the production floor.
Advantages of Industrial Prototyping for Large-Scale Manufacturing
-
Cost Efficiency in Production Setup
One of the most significant benefits of industrial prototyping is cost savings. By thoroughly testing prototypes, companies can prevent expensive mistakes during the mass production phase. For instance, Wiesel’s prototyping services allow clients to experiment with different materials, production techniques, and assembly processes to determine the most cost-effective approach. Identifying these variables during prototyping reduces the need for adjustments later on, streamlining the production line setup and lowering overall production costs.
-
Enhanced Product Quality and Performance
Prototyping allows for rigorous quality control before the full-scale production phase begins. This process is essential in industries that demand high-performance standards, such as aerospace and medical devices, where any defect could lead to significant repercussions. By collaborating with Wiesel, manufacturers can ensure that their prototypes meet stringent quality requirements and are optimized for high performance. Wiesel’s prototyping solutions also incorporate advanced testing, allowing companies to make necessary adjustments and deliver end products that excel in durability, functionality, and precision.
-
Improved Manufacturing Flexibility
In today’s market, flexibility is essential for manufacturers to respond to changing customer demands quickly. Prototyping enables companies to adapt their designs and production processes to align with new requirements. Wiesel supports this flexibility by offering rapid prototyping options, including 3D printing, CNC machining, and other additive manufacturing techniques. These methods allow clients to explore multiple design iterations and make quick changes, giving them the agility needed to remain competitive in dynamic markets.
-
Reduced Time-to-Market
Speed is critical in industries where product lifecycles are short, and market windows narrow. Prototyping can significantly reduce the time-to-market by identifying and resolving design or production issues early. Wiesel’s rapid prototyping services streamline the design and testing phase, enabling companies to bring their products to market faster. For example, a consumer electronics company using Wiesel’s services can move from concept to production in weeks instead of months, gaining a crucial advantage in a fast-paced industry.
-
Sustainable Manufacturing Practices
As companies across all sectors seek to reduce their environmental footprint, industrial prototyping plays a vital role in sustainable manufacturing. By minimizing waste through early testing and refinement, Wiesel helps companies adopt eco-friendly practices that are both cost-effective and environmentally responsible. By reducing the number of iterations needed in production and ensuring efficient use of resources, prototyping aligns with the growing demand for sustainable manufacturing processes.
Technologies Enabling Effective Industrial Prototyping
Wiesel leverages a range of advanced technologies to ensure prototyping meets the demands of modern large-scale manufacturing:
-
3D Printing and Additive Manufacturing: Ideal for creating complex, highly detailed prototypes quickly, 3D printing offers flexibility in material choice and precision in design. Wiesel’s 3D printing capabilities support a wide array of materials, from polymers to metals, allowing companies to assess both function and aesthetics with ease.
-
CNC Machining: CNC machining is indispensable for producing high-precision parts, particularly for industries where tolerances are tight. Wiesel’s CNC capabilities enable clients to create prototypes that closely mimic the final product, allowing for thorough testing under real-world conditions.
-
Digital Simulation and CAD Modeling: Digital simulation tools help identify potential issues in design before any physical prototype is created. Wiesel’s use of simulation software allows companies to model product performance and manufacturing efficiency, leading to a more streamlined prototyping process.
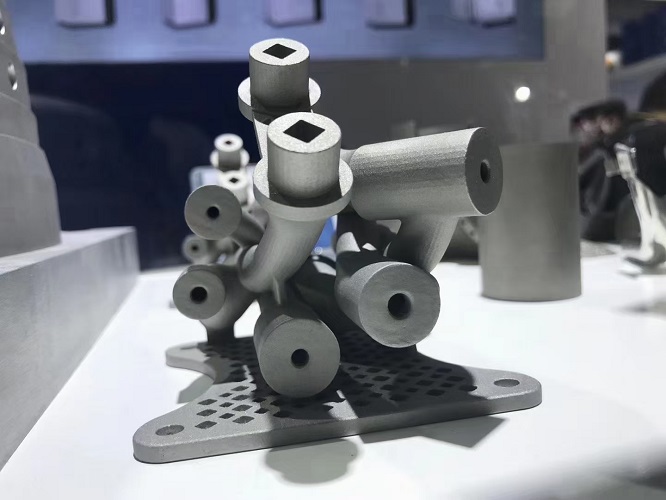
Case Study: Wiesel’s Impact in the Automotive Industry
One of Wiesel’s recent projects involved a large automotive manufacturer developing a new engine component. The client needed a durable, heat-resistant part that could withstand extreme conditions, but initial designs raised concerns over the material's longevity. By leveraging Wiesel’s prototyping services, the client was able to test multiple material options, refine the component’s design, and verify its durability through simulations and physical testing. This collaboration not only accelerated the development process but also minimized material waste, reducing production costs significantly.
Conclusion
Industrial prototyping is indispensable to successful large-scale manufacturing, and companies like Wiesel are at the forefront of this innovation. By enabling cost savings, improving quality, and enhancing flexibility, prototyping supports the development of robust products ready for mass production. Whether working in automotive, medical, aerospace, or consumer electronics, Wiesel’s expertise ensures that manufacturers can bring products to market quickly, efficiently, and sustainably. Through continuous innovation in prototyping technology, Wiesel is helping companies stay competitive and adaptable in an ever-evolving manufacturing landscape.